Tubes and Pipes
Electric Resistance Weld
This kind of pipe is produced from individual sheets or continuosly from rolls of skelp.
The EWR pipe is cold formed into a cylindrical shape and electric current is used to heat the edges of the strip for the fusion weld. Revolving copper discs serve as electrodes and raise the temperature to about 1426℃ for effective welding.
Spiral Submerged Arc Welded
This type of spirally welded steel pipe is produced by using the double-sided submerged arc welding method. Spiral welded pipes are formed using narrower plates or hot rolled coils. The spiral welding process permits the production of large-diameter pipes suitable for transporting large volumes of oil and gas.
From Φ219mm-Φ3000mm and wall thickness from 6mm to 25mm the double-sided submerged arc welding processing boasts not only high deposition rate, but also deep penetration ability, good quality and appearance of welding line and high density.
Longitudinal Submerged Arc Welded
This are basically pipes formed by bending rectangular steel plates and are subsequently welded longitudinally(internally and externally) along the seam to form a pipe.
With an outside diameter from 406.4mm to 1422.4mm, wall thickness from 6mm to 50mm, unit length from 3m to 12.5m our LSAW pipes can be produced from materials like carbon steel, special type steel and low alloy steel with grades up to max X80.
A pipe is a tubular section or hollow cylinder, usually but not necessarily of circular cross-section, used mainly to convey substances which can flow — liquids and gases (fluids), slurries, powders, masses of small solids. It can also be used for structural applications. In common usage the words pipe and tube are usually interchangeable, but in industry and engineering, the terms are uniquely defined. Depending on the applicable standard to which it is manufactured, pipe is generally specified by a nominal diameter with a constant outside diameter (OD) and a schedule that defines the thickness. Tube is most often specified by the OD and wall thickness, but may be specified by any two of OD, inside diameter (ID), and wall thickness.
The seamless steel pipe manufacturing process starts with a solid, round steel billet. This billet is then heated to great temperatures and stretched and pulled over a form until it takes the shape of a hollow tube, there are some great advantages to making a pipe in this way.
Benefits of the seamless pipe and tube:
-
Increased Pressure Ratings The greatest advantage of seamless steel pipes is their increased ability to withstand pressure. Although seamless pipe can sometimes be more expensive than welded pipe, this increased ability to withstand pressure allows you to use pipes that are thinner and lighter, which can help cut down on expenses.
-
Uniformity of Shape Seamless steel pipe is a continuous extrusion of the alloy, meaning that it will have a round cross section that you can count on, which is helpful when you’re installing pipes or adding fittings.
-
Strength Under Loads Seamless steel pipe can sometimes be more expensive than other forms of steel pipe, but it’s also more reliable. This is because it has greater strength under loading. Empty pipe must always support its own weight, but when a pipe is filled with material–or under load–it must also support that weight as well.

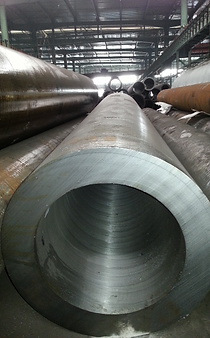
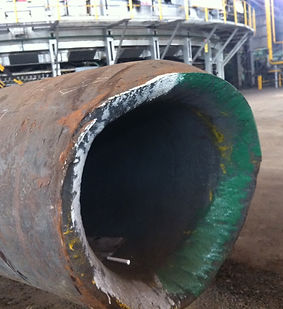
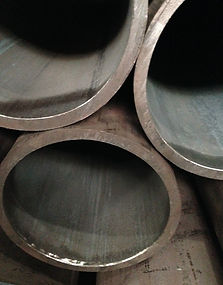
Seamless Tubes and Pipes
Welded Tubes and Pipes
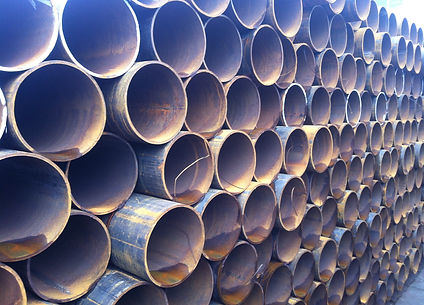
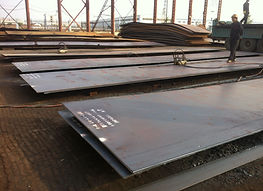
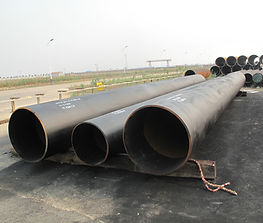
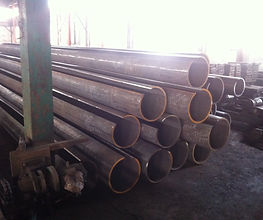


Main materials:
● Carbon Steel
● Alloy Steel
● Stainless Steel
● Titanium
Main standards and grades:
● ASTM SA53 -106 Gr.B & C / A335P11-P5-P12-P22-P91 / B338,B861,B862/SA179,192, TP304, TP316
● API5L Gr.B X42,X52,X60,X65,X80
● API5CT H40,J55,K55,N80,N80Q,L80
Main applications:
● Line pipe
● Heat exchange
● Low / Medium / High pressure boilers
● Special corrosive environment
● High temperature environment
Main industries:
● Offshore and onshore oil exploitation
● Nuclear and thermal power plants
● Petrochemical
● Chemical
● Ocean engineering
We have covered a big range of products in seamless and welded condition from several grades and kinds of materials that can be used for different applications as followings:
Welded pipes have been a common structural element in the construction industry for decades. They are versatile in their ability to solve many complex construction problems. Used as structural elements, in combination walls, as casings or as water transportation, the applications are infinite and also welded pipes can be used in many industries specially the oil and gas. Some of the advantages are:
-
Cost-effectiveness
-
Strength A cold forming gives a welded tube or pipe a higher yield and tensile strength than the steel from which it is made.
-
Wide size range The ability to produce pipes in long lengths due to continuous raw material rolling ability and an exceptionally broad range of OD and wall thickness dimensions
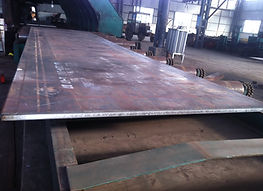
For more on our steel tubes and pipes, other products or any other service we provide, please contact us we will be more than happy to hear from you.
About us
Contact us
2014. This site was created by The OILSO Team
These benefits make seamless steel pipes the preferred material in an array of commercial pipe applications, including ship building, pipelines, oil rigs, oil field equipment, pressure vessels, machinery parts and offshore rigs. An additional benefit of seamless pipes is that they perform well in harsh conditions, which means that they can be used in extremely cold or hot environments.